Computational Fluid Dynamics,
or CFD, uses advanced computer software to model the flow of fluids
through a processing facility. The fluid may be in liquid, gas or solid
form, or a combination of them. Using computer simulation a wide range
of variations in physical design and operational parameters can be
tested and refined until a set which gives optimum performance is
identified. The broad application of CFD to new and
existing plant in the chemical industries, mineral processing, metal
production and energy industries has the potential to save companies
many millions of dollars per year.
In recent years, our focus research has been to develop and validate the
multi-phase CFD models for various mineral processing units
like dense medium cyclones (DMC), hydrocyclones (HC), feed
slurry distributors and flotation devices. In
particular, extensive results have been obtained on the detailed
multi-phase flow in DMC/HC devices in terms of air-core resolution, mean
and turbulence flow field analysis, turbulent dispersion analysis w.r.to
particle classification and understanding the classification mechanism.
Extensive CFD validation is also carried out by using the data collected
by adopting various experimental techniques; LDA used
for the measurement of mean and turbulent flow field, Gamma ray
tomography(GRT)/Electrical resistance tomography (ERT) used for
the measurement of solids concentration and air-core profiles, physical
cyclone experiments used for quantifying the fish hook effect
of hydrocyclones at fine size fractions, sampling probe
for the collection of solids distribution inside a cyclone, Dubex/
RHEOLOGICA/Tube viscometers used for the
characterization of
mineral slurries viscosities.
Further these CFD multi-phase models were used to design the new
efficient separation equipments for example a TATA-JK dense medium
cyclone for treating the fine coal (-2 +0.25mm) having high NGM (near
gravity materials) in a collaboration with JKMRC, University of
Queensland and a new feed distributor for the TATA Steels coal
preparation plant having gravity feeding to DM Cyclones. Improved
mathematical models based on industrial historical data and inputs from
CFD are also developed using non-linear model building methods
for hydrocyclones, which would be part of JKSimMet
newer version of mineral processing simulator. Also working on
waste utilization/recovery of mineral matter from low grade
minerals like low grade iron ore/iron ore slimes through
innovative/novel mineral beneficiation research.
|
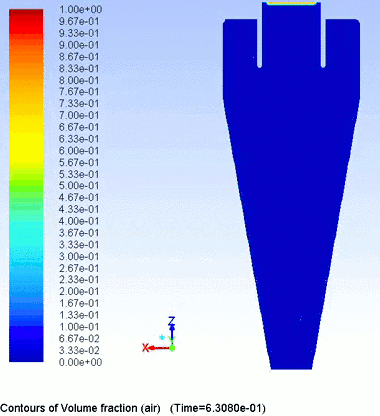
Air-core formation in 350mm DMC
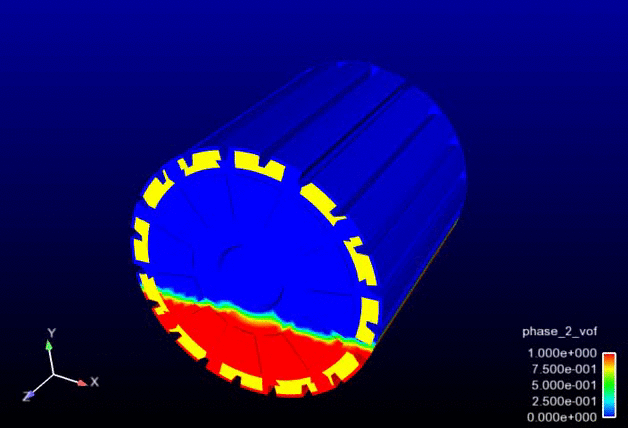
Flow in a Ball mill |